August 24, 2022 GENERAL
Maritime Fairtrade interviews Baki Lee, director of PT Global Expo Management, organizer of INAMARINE, Indonesia’s largest tradeshow for the maritime and offshore industry.
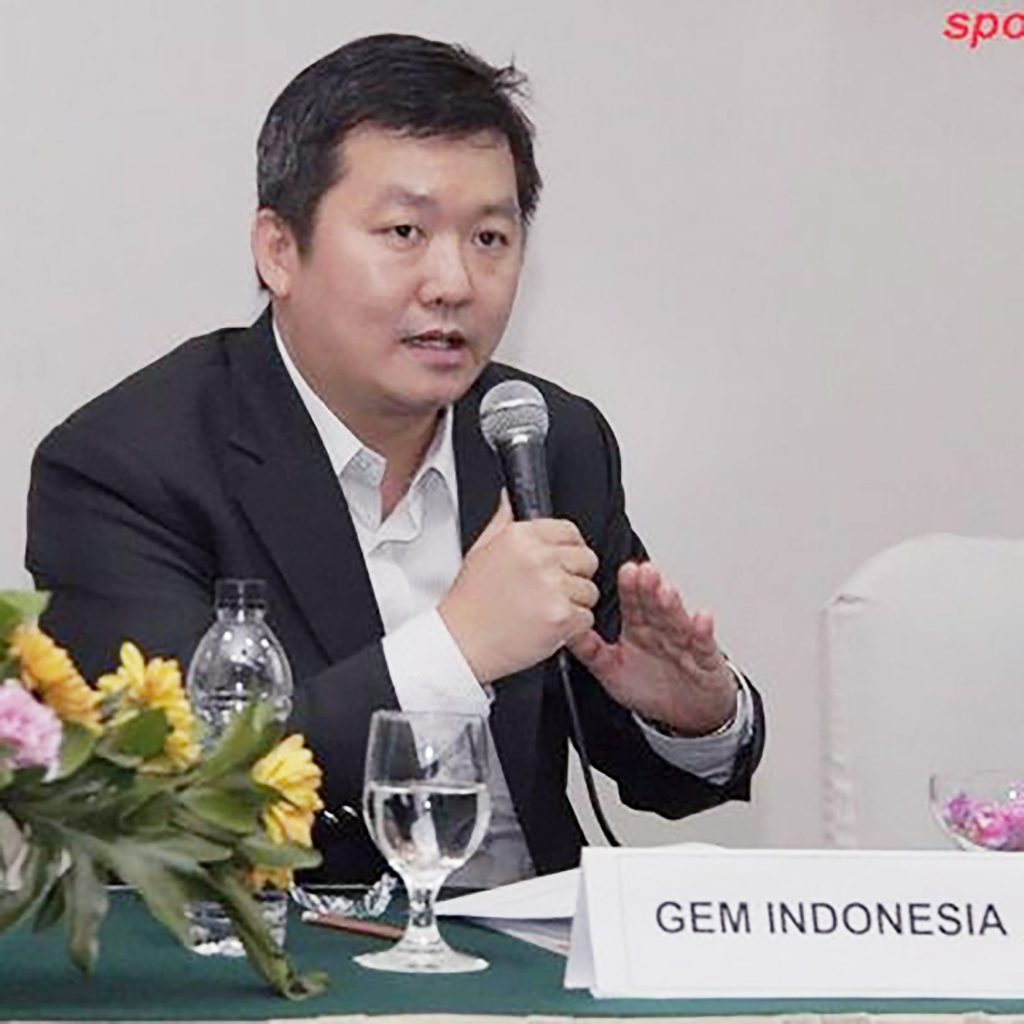
What is your opinion of the current state of the Indonesian economy and the general job market?
Indonesia’s economic activity is gradually returning to normal, and COVID-19 infections are under control. The prediction for Indonesia’s growth in 2022 has increased from 5.0 percent to 5.2 percent, portraying strong domestic demand and exports. Private consumption is being improved by gains in employment, income, and confidence.
Despite global inflationary pressures and recession concerns, Indonesia’s economy increased significantly in the second quarter, demonstrating that the recovery trend is continuing and even strengthening.
What are some special trends and outlooks that you noticed about the Indonesian maritime industry?
As the largest archipelagic country in the world, the shipping industry is the infrastructure and
backbone of the life of the nation and state. Indonesia has a grand design to establish Sea Toll Programs to improve connectivity, by increasing the capacity of 24 seaports.
Currently, the competitiveness and share of cargo for the national fleet is still relatively low. The shipbuilding industry, which is actually very strategic because it has a long upstream-downstream chain, has yet to develop. The current port system only acts as a branch or branch of Singapore or other overseas ports. It is hoped that the construction of some big seaports can increase the competitiveness of national shipping in the future.
Specifically, how is the job market for the maritime industry doing?
The government has unveiled Indonesia Vision 2045, a long-term strategy that aims for Indonesia to have a GDP of US$7.3 trillion, ranking fifth or fourth in the world. For instance, it is anticipated that the maritime industry will contribute 12.5 percent of Indonesia’s GDP. If Indonesia is successful in achieving this aim, additional employment possibilities will exist.
Why do you think a career in the maritime industry is attractive?
With more than 12 million employees, the maritime sector is one of the most significant sources of employment for the Indonesian economy. As the sector develops in Indonesia, there is also room for further job creation.
What do you think are the top five well-paid jobs in the maritime industry?
Five of the best jobs: Oceanographer, naval architect, marine engineer, welding engineer and drilling engineer.
What is the starting salary for a fresh grad entering the maritime industry?
For a ship technician, starting salary is usually IDR4,804,236 and IDR40,573,749 net per month (US$322 to US$2,721).
What is your advice for a fresh grad wanting to join the maritime industry?
One of the fields of vocational education that has contributed to the acceleration of Indonesia’s economic recovery is the maritime sector. The success of this maritime vocational education is proven through graduates who really answer and meet the challenges of the international maritime world of work.
Fresh graduates who want to enter the maritime industry must be equipped with additional skills such as computers, presentation skills and problem solving in addition to mastering English.
Source: https://maritimefairtrade.org/guide-to-indonesias-maritime-industry/